Introduction to Fleet Heater Maintenance
Having a properly functioning heater system is critical for fleet vehicles being operated in colder climates. As a fleet manager, keeping your heaters in top working order should be a top priority to ensure driver safety and comfort. Performing regular maintenance and repairs on fleet heaters will save money over the long run by preventing major issues from developing.
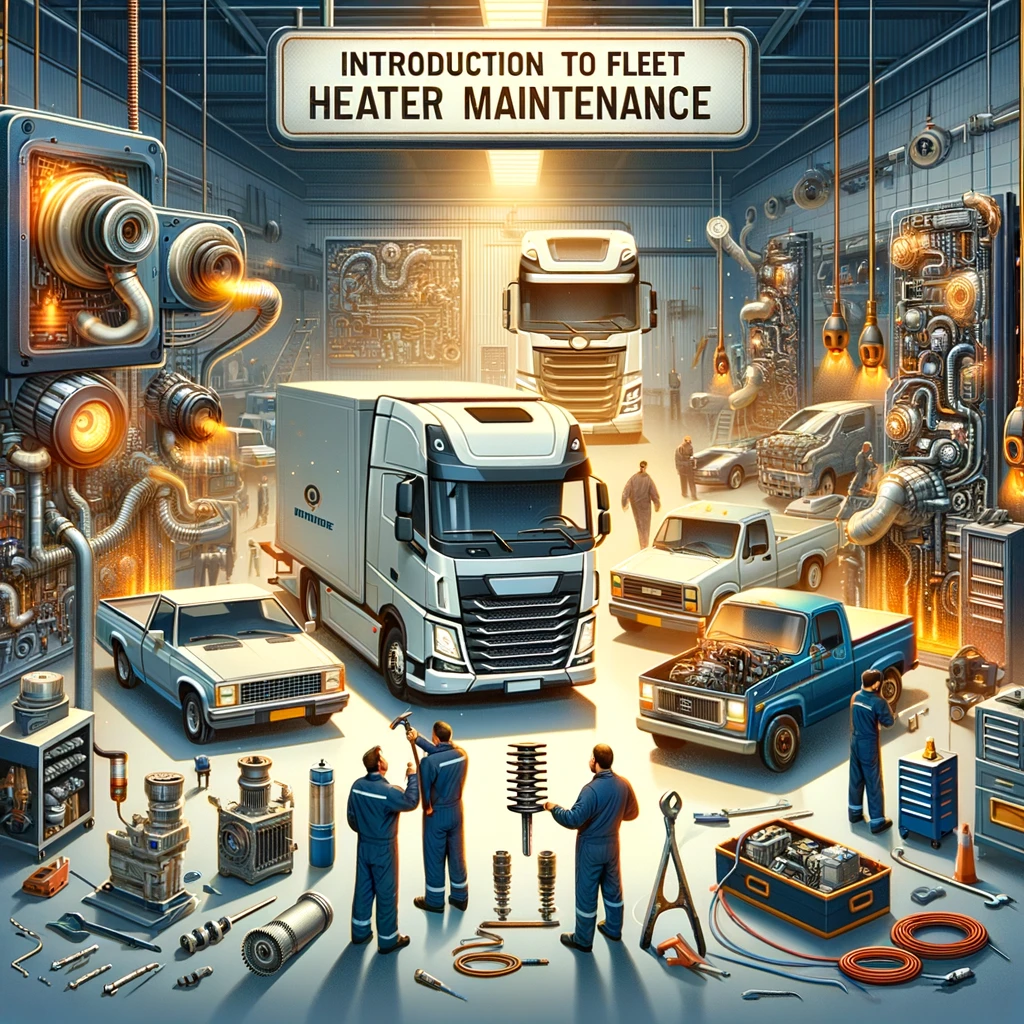
In this comprehensive guide, we will explore all aspects of fleet heater maintenance and repair. Proper heater care requires diligence but pays dividends through improved driver productivity, reduced downtime, and lower costs. By following the tips outlined here, you can optimize your maintenance program to achieve peak heater performance.
The Importance of Regular Maintenance for Fleet Heaters
Heater systems in fleet vehicles take a lot of abuse during cold weather operations. Frequent use, vibration, dirt, and normal wear and tear can all cause heaters to degrade over time. That’s why regular maintenance is critical for ensuring heaters remain in proper working order.
When heaters fail, it impacts driver safety, comfort, and productivity. A recent survey showed that a non-functioning heater resulted in an average productivity loss of 45 minutes per truck per day. Multiply that across an entire fleet, and it really adds up.
By performing routine heater system inspections and repairs, you can avoid the costs of downtime and driver dissatisfaction. Technicians should inspect heaters at least annually, or more frequently for vehicles in severe service.
During regular maintenance, all components should be checked, including heater cores, hoses, thermostats, blower motors, ductwork, and controls. Catching small issues early prevents them from turning into major headaches down the road.
An ounce of prevention is truly worth a pound of cure when it comes to fleet heater maintenance. Investing a modest amount of time and money in routine upkeep will pay back tenfold through improved reliability and lower lifetime repair bills.
Common Issues with Fleet Heater Systems
To maintain your fleet’s heaters properly, it helps to understand the most common problems technicians encounter:
- Clogged heater cores: Built-up debris causes restricted coolant flow and heat transfer. Flushing the system regularly prevents this.
- Leaky hoses: Age, vibration, and clamp deterioration can cause coolant leaks at hose connections.
- Sticking thermostats: Corrosion and deposits cause thermostats to not open fully or close completely.
- Blower motor failure: Brush and winding wear will eventually cause blower motors to stop working properly.
- Duct leaks: Cracks or detachment causes hot air leaks, reducing heating efficiency.
- Control cable issues: Over time, control cables can stretch, fray, or break, leading to loose connections.
- Fuel line/injector faults: On diesel vehicles, these issues affect fuel delivery to the burner assembly.
- Burner problems: Gas heater burners are susceptible to corrosion and carbon build-up.
By proactively identifying and addressing minor issues before they escalate, fleet managers can optimize heater uptime. Technicians should be on the lookout for these common failure points during inspections.
Checking Heater Core Condition and Flushing the System
The heater core is essentially a small radiator that utilizes hot coolant from the engine to warm cabin air. Checking its condition and flow is one of the most critical maintenance items for fleet heaters.
Over years of use, rust, dirt build-up and scaling can restrict coolant flow through the narrow tubes in the core. This causes a notable reduction in heating performance.
During each maintenance interval, technicians should visually inspect the heater core tubes for debris build-up. Coolant should flow freely when drained from the system.
An easy way to identify flow restriction is to check the temperature differential across the core. If the outbound coolant is not getting adequately cooled, that indicates reduced flow.
For preventive maintenance, you should flush the heating system at least once per year. This removes accumulated sediment and scale that could eventually block the core. Use a commercial coolant system flush, and connect it per the manufacturer’s instructions.
Replacement of old and contaminated coolant is also advised to maintain proper chemical balance. Your coolant should be tested annually as part of a comprehensive maintenance program.
Inspecting Hoses, Clamps, and Seals for Leaks
The extensive network of coolant hoses that serve the heater core are prone to age-related cracking and loosening. Small leaks can quickly turn into major repairs if not addressed promptly.
Check all heater hose connections for dampness or stains. Tighten any loose clamps, and watch for deterioration of the hose ends. It helps to gently twist and manipulate the hoses while inspecting them.
Also, examine where hoses pass through the firewall for signs of leaks. Any moisture here indicates a bad seal that needs to be resealed with fresh silicone. Loose firewall grommets can also admit exhaust gases into the cabin.
Planning ahead, you may want to proactively replace older coolant hoses during scheduled maintenance intervals. This avoids situations where hoses let loose unexpectedly after years of slow deterioration.
Use only high-quality, OEM-approved replacement hoses. Check compatibility information to make sure clamps and fittings match properly. This prevents leaks and potential engine overheating.
Testing the Thermostat and Temperature Sensors
To control cabin heating, the thermostat and coolant temperature sensors must be in good working order. Faulty stats and sensors will deliver incorrect temperature readings and signals.
During maintenance, remove and test thermostats for proper opening and closing operation per the manufacturer’s specifications. Thermostats should be replaced as a precaution every 3-4 years to prevent sticking.
The coolant temperature sensor that inputs readings to the HVAC module should be tested for accuracy. Compare its readings against an external thermometer on the coolant lines. Replace sensors that are out of calibration.
Make sure to use OEM or OEM-approved replacement thermostats and sensors. Aftermarket or universal parts often have poor tolerances that impact system performance and reliability.
Cleaning Heater Boxes and Ductwork
Cabin air filters only catch some of the dirt and debris that would otherwise end up inside the fleet heater system. Over years of service, a notable buildup can accumulate inside the heater boxes and ductwork.
Remove and inspect the heater/evaporator housing annually to check for dirt buildup. Use compressed air and vacuum tools to dislodge and capture any debris present. This improves air quality and heat transfer.
Also, check that cabin air ducts are clear by shining a bright flashlight inside. Look for any obstructions or foreign material that may have fallen or accumulated inside the ducting.
Repair any loose, cracked, or disconnected ducts that could allow hot air leaks. Use OEM-approved seals and adhesives to patch any damaged sections or joints.
Proper duct sealing improves heating efficiency and allows climate control systems to maintain the desired cabin temperatures.
Replacing Cabin Air Filters
Cabin air filters provide the all-important function of removing dust, pollen and other airborne contaminants from entering the passenger compartment. But when clogged with debris, they can greatly restrict airflow.
Inspect and replace cabin air filters at least annually. Checks should be more frequent for vehicles operated in dusty or polluted environments.
For maximum effectiveness, always replace with OEM or OEM-equivalent filters. Avoid cheap aftermarket filters that may not seal properly. Proper fit and sealing prevent air bypass.
When installing the filter, make sure the airflow arrow points in the right direction for your vehicle. Double check the filter housing for tight sealing to prevent unfiltered air entry.
Clean cabin air filters mean better heating performance, defrosting, and climate control for improved driver comfort and safety.
Checking the Condition of Blower Motors and Fans
The blower motor and fan comprise the heart of the air delivery system for heaters. When these components degrade, it dramatically reduces heating airflow and performance.
Inspect blower motors and fans for proper operation. Check for excess noise, binding, and slow running speed. Test them on all fan settings.
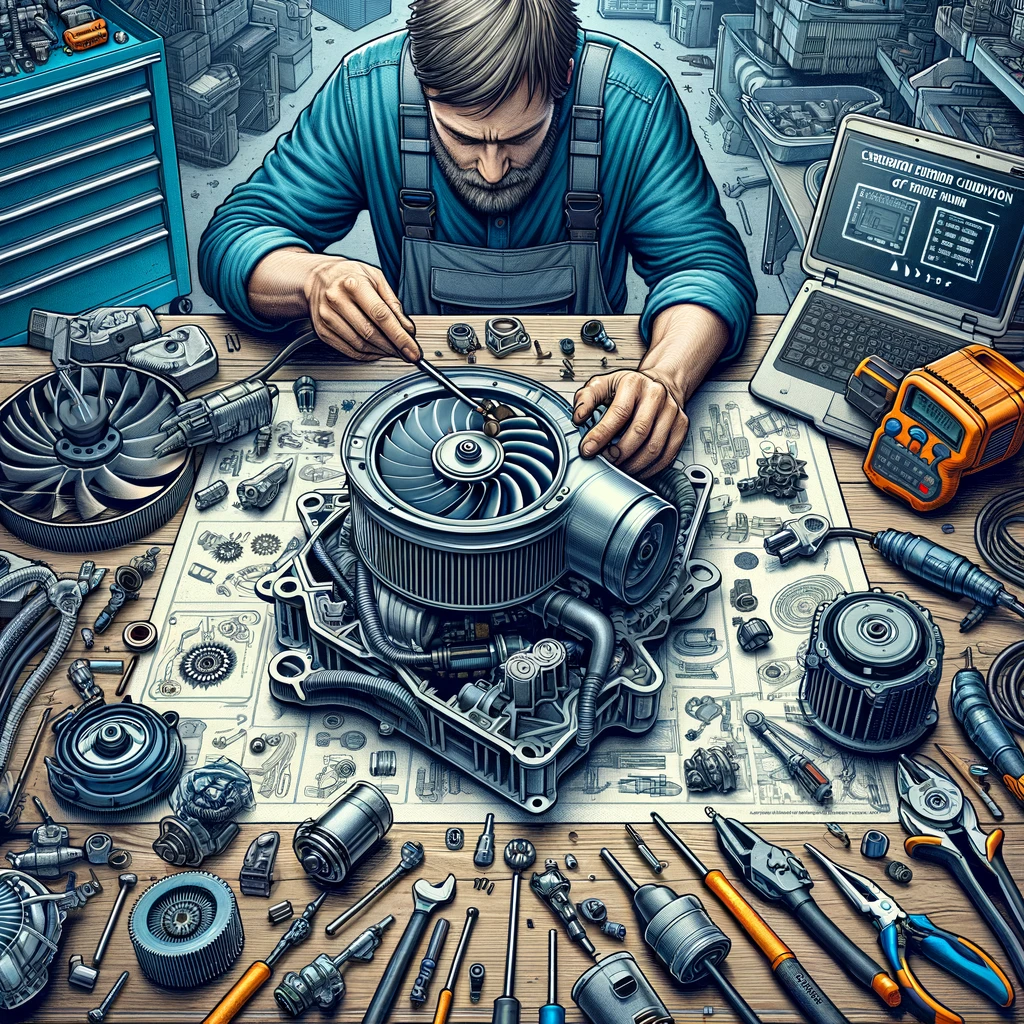
If equipped, check the function of the blower resistor that controls fan speeds. Broken resistors can limit blower speeds.
Lubricate blower motor shafts with approved electric motor oil. Clean fan blades of any debris buildup. Watch for cracks in plastic fan blades.
Plan for blower motor replacement every 5-6 years for preventative maintenance. Hard use in severe service may necessitate more frequent replacement.
Inspecting Exhaust Pipes and Manifold for Leaks
Diesel air heaters utilize hot exhaust gases to provide supplemental heat. Exhaust leaks downstream of the diesel particulate filter can allow dangerous carbon monoxide to enter the cabin.
Carefully inspect the exhaust piping, the DPF, and the exhaust manifold for any leaks or cracks. Repair minor leaks with approved high-temp sealants. Replace any sections with severe corrosion damage.
Also, check exhaust hanger mounts and brackets for damage that could lead to the exhaust shifting out of position. Broken hangers lead to further damage.
Proper repairs will prevent deadly CO leaks in the cabin area. It also keeps the heating system working at peak efficiency for the best heat output.
Troubleshooting Loss of Heat Issues
When fleet heaters underperform or stop producing sufficient warmth, it’s typically due to one of these main problems:
- Low coolant level
- Coolant flow blockage
- Blower fan failure
- Thermostat stuck closed
- Leaking heater core
- Duct leak or obstruction
- Control cable malfunction
- Fuel delivery issues (diesel)
- Burner failure (gas)
Thorough troubleshooting involves systematically checking each component starting with coolant level and flow. Inspect fans, thermostats, cores, ducts, and controls to isolate the issue.
For diesel air heaters, verify fuel system operation and exhaust integrity. On gas engine heaters, inspect burners and fuel injectors.
Many problems can be fixed with basic tools and repairs. But don’t delay diagnosis, as loss of heat impacts driver safety and productivity.
Diagnosing Blower Motor Failure
When the blower fails, hot air can’t circulate through the core into the cabin. The first step is to listen and feel for motor operation when the fan switch is activated.
If the motor is silent and not spinning, check the electrical connections and voltages at the blower motor plug. Clean any corroded contacts and replace burnt terminals.
Use wiring diagrams to test each blower speed circuit for power and ground. If voltage is present, the motor windings or brushes are likely faulty, necessitating replacement.
For blowing motors that run erratically or seize up, the internal bearings are probably worn out. Try lubing the shaft, but replacement is often required in those cases.
Proper diagnosis of blower motor issues reduces troubleshooting time and gets heat blowing again quickly.
Fixing Stuck Thermostats
A thermostat stuck in the closed position prevents coolant circulation through the heater core. This deprives the system of that crucial heat source.
Remove and inspect the thermostat whenever heat issues arise. Check for freedom of movement and proper opening temperature.
Clean thermostats using approved solvents or mild abrasives to remove mineral deposits that can impede motion.
Replace thermostats that fail to open properly or don’t seal well in the closed position. Use OEM or OEM-equivalent parts to maintain proper system control.
Make sure to check thermostat gaskets and housings for warping or deterioration that could hinder proper functioning.
Repairing Leaky Heater Cores
The heater core is designed to last the service life of most fleet vehicles. However, corrosion and damage can lead to leaks over time.
For minor leaks, carefully clean the core passages and reseal them with approved epoxy compounds. More extensive leaks require complete core replacement.
Use extreme care when handling heater cores, as the fins and tubes damage easily. Proper removal and installation techniques are critical.
Thoroughly flush the cooling system after repairs to clear any contamination from the leaking core. Always use new clamps and gaskets with replacement cores.
Proper heater core repair eliminates the need for continual coolant top-offs while keeping windows clear and the cab warm.
Replacing Broken Control Cables
Heater system control cables operate dampers, switches, and motors to regulate temperatures. Over time, the inner cables can fray or break from bending and vibration.
Inspect control cables for smooth operation. Check for excessive looseness indicating stretched cables.
Replace any corroded or damaged cables. Carefully disconnect old cables from control levers and pulleys, and route new ones along the same paths.
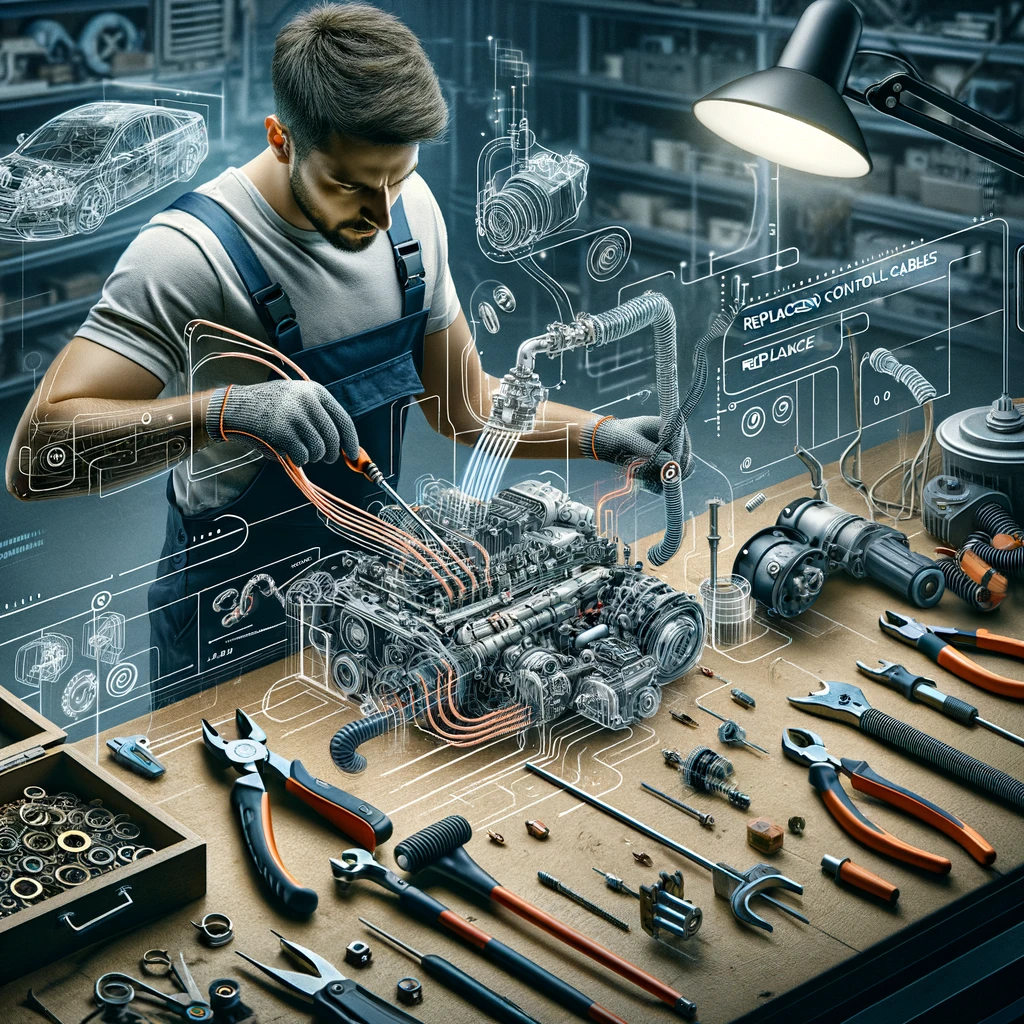
Adjust cable tension as needed to deliver full travel without binding. Verify full hot/cold range before reassembly.
Smoothly operating control cables are needed to maintain cab comfort and prevent system damage. Handle cables with care to maximize durability.
Checking Fuel Lines and Injectors
Diesel-fired auxiliary cabin heaters rely on a supply of clean diesel fuel for combustion. Contaminated or leaking lines and bad injectors can lead to heater performance issues.
Carefully inspect fuel supply lines for damage or leaks. Check for abrasion, cracks, or excessive hardening. Replace deteriorated sections of the line.
Make sure fuel system filters are clean and valves are functioning properly. Flush injectors and lines if necessary to remove contamination.
Properly operating fuel components are critical for clean combustion and heat output. Use OEM parts designed specifically for diesel auxiliary heater applications.
Bleeding Air from Diesel Heater Systems
Air trapped in the fuel lines of diesel-fired heaters prevents proper fuel delivery. This leads to rough starting, misfiring, and reduced heat output.
Follow the manufacturer’s procedures to bleed air from the system after any service work. This typically involves loosening injector lines to allow fuel flow until air is purged.
Check for air leaks on the suction side of the fuel pump. Small leaks introduce air into the system leading to future airlock.
Proper bleeding eliminates hard starting and rough operation while restoring full heat performance. It’s critical for reliable operation in cold weather.
Overhauling Gas Heater Burner Assemblies
Gasoline-powered auxiliary heaters rely on clean burner assemblies for proper fuel combustion. Carbon buildup and component wear reduce heating efficiency over time.
Periodically overhaul burner assemblies by disassembling, cleaning, and inspecting components. Replace worn orifices, valves, and igniters.
Look for any cracks or leaks in the burner housing. Make sure fuel filters and lines are clear. Adjust fuel pressure and combustion air to spec.
Properly overhauled burner assemblies ensure peak heating performance and efficiency. Sticking valves and weak igniters lead to hard starting issues.
Sourcing Quality Replacement Parts
Reliable heaters start with using top quality replacement components approved by the OEM. Cheap aftermarket parts often don’t last or perform well.
Only use OEM or OEM-equivalent parts from reputable suppliers for critical items like heater cores, thermostats, sensors, motors and burner assemblies.
Make sure replacement hoses and clamps meet all size, pressure rating and temperature requirements for the application.
Check component specs and tolerances against OEM parts during sourcing. Properly researched parts increase uptime.
Understanding Heater Warranties and Service Contracts
Fleet heater repairs can carry high parts and labor costs. That’s why warranty coverage and service contracts are valuable for budgeting and reducing operating expenses.
- OEM warranties cover defects for a set time period. However, they have limitations on scope, length, and transferability.
- Extended warranties provide longer coverage but add to vehicle purchase costs. Review terms closely.
- Maintenance contracts provide defined repairs/services for a fixed monthly fee. They help control expenses.
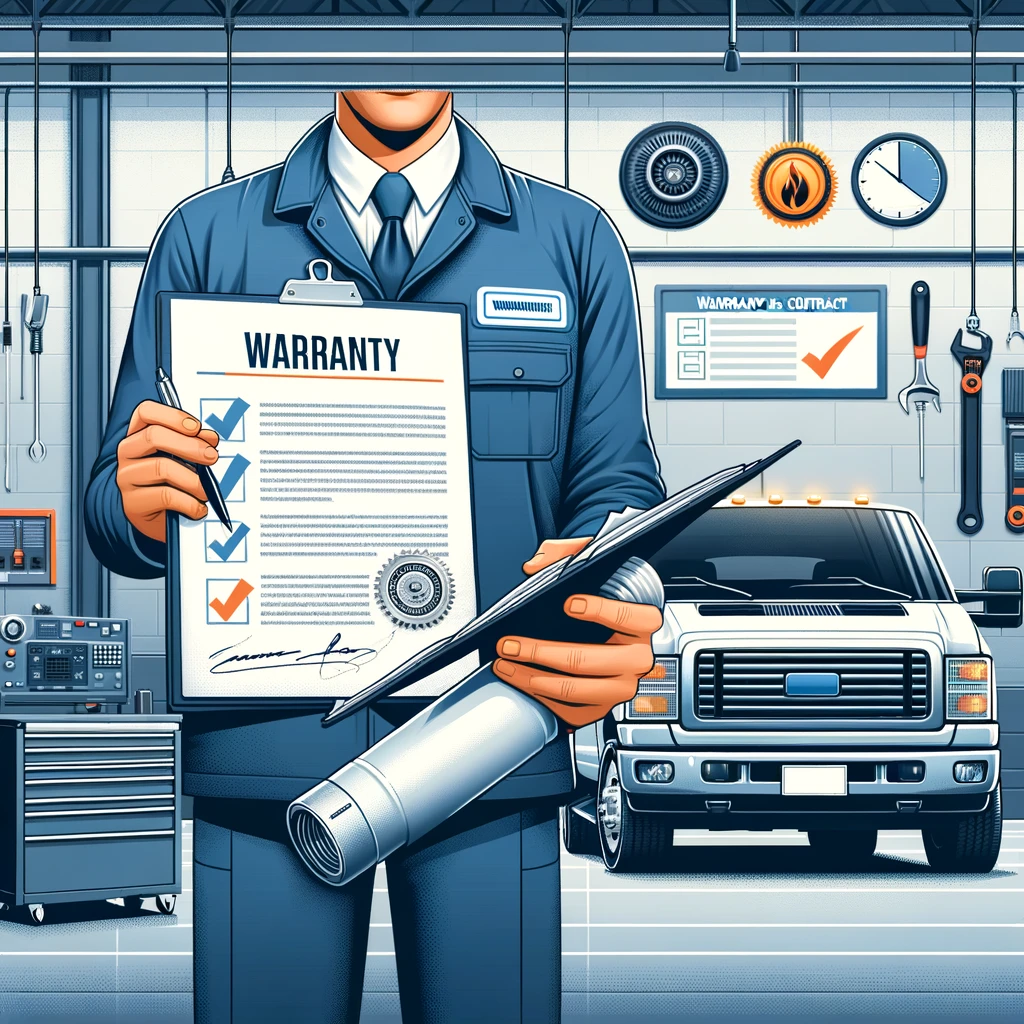
Evaluate the costs versus benefits of all service agreements carefully before purchasing. Understand exactly what is and isn’t covered.
Developing a Fleet Heater Maintenance Schedule
Preventative maintenance is key for fleet heaters. Develop a comprehensive schedule that covers inspection, testing and service tasks at regular intervals.
Define specific procedures to be performed at designated mileages or hourly operation intervals. Assign trained personnel to execute each task.
Track completion of scheduled services for all vehicles. Software programs can generate reminders and compliance reports.
Continuous improvement of the maintenance schedule ensures it aligns with component life cycles and fleet utilization patterns.
Documenting scheduled maintenance provides legal records of proper fleet care. Well-maintained heaters also retain higher resale value.
Training Technicians on Proper Heater Repairs
Improperly performed heater repairs often lead to comebacks and repeat failures. Investing in technician training improves repair quality and prevents bigger issues later on.
Partner with OEM component suppliers to hold regular technical training sessions on current heating systems. Include hands-on troubleshooting and repair instructions.
Enroll key technicians in specialized heating and climate control certification programs. Continuing education expands expertise.
Fleets with well-trained technicians have fewer repeat repairs and enjoy better heating system reliability. Allow time and funding for proper training.
Investing in Diagnostic and Specialty Tools
Accurate troubleshooting and efficient heater repairs require using the right diagnostic tools and specialty equipment. Invest to equip your shop properly.
- Handheld diagnostic scanners and heating system testers speed fault code diagnosis.
- Coolant system vacuum fillers and pressure testers help bleed and check for leaks.
- Core, hose, and clamp removal tools prevent damage to components.
- Nitrogen welding equipment enables aluminum core and pipe repairs.
Allocate a budget annually to upgrade tools and capabilities. Proper equipment reduces technician labor hours and mistakes.
Keeping Detailed Maintenance Records
Meticulous recordkeeping is crucial for tracking fleet heater repairs and establishing maintenance patterns. Records should include:
- Vehicle data like VIN, mileage, and operating hours
- Complete descriptions of repairs performed
- Parts and materials used, with invoices attached
- Technician notes on symptoms and diagnostics
- Scans of diagnostic trouble codes
Keep physical folders or use a maintenance software system to organize records and generate reports. Detailed histories help determine root causes and optimize maintenance plans.
Keeping Detailed Maintenance Records
Meticulous recordkeeping is crucial for tracking fleet heater repairs and establishing maintenance patterns. Records should include:
- Vehicle data like VIN, mileage, and operating hours
- Complete descriptions of repairs performed
- Parts and materials used, with invoices attached
- Technician notes on symptoms and diagnostics
- Scans of diagnostic trouble codes
Keep physical folders or use a maintenance software system to organize records and generate reports. Detailed histories help determine root causes and optimize maintenance plans.
Monitoring Heater Condition with Telematics
Onboard telematics systems provide continuous monitoring of vehicle systems between maintenance intervals. Many fleets now utilize telematics to enhance heater oversight.
Fault code alerts pinpoint issues needing immediate attention. Diagnostics can even be performed remotely in some cases.
Real-time temperature readings identify loss of heat situations so drivers can be instructed to a service location.
Long term data logging reveals heating system patterns and aids predictive analytics. Anomalies signal developing issues.
Implementing a telematics program improves maintenance efficiency, reduces downtime, and enhances heating system reliability.
Prioritizing Heater Maintenance in Cold Weather
Once freezing temperatures arrive, diligent heater system care becomes absolutely crucial. Make heaters the top maintenance priority to keep vehicles on the road.
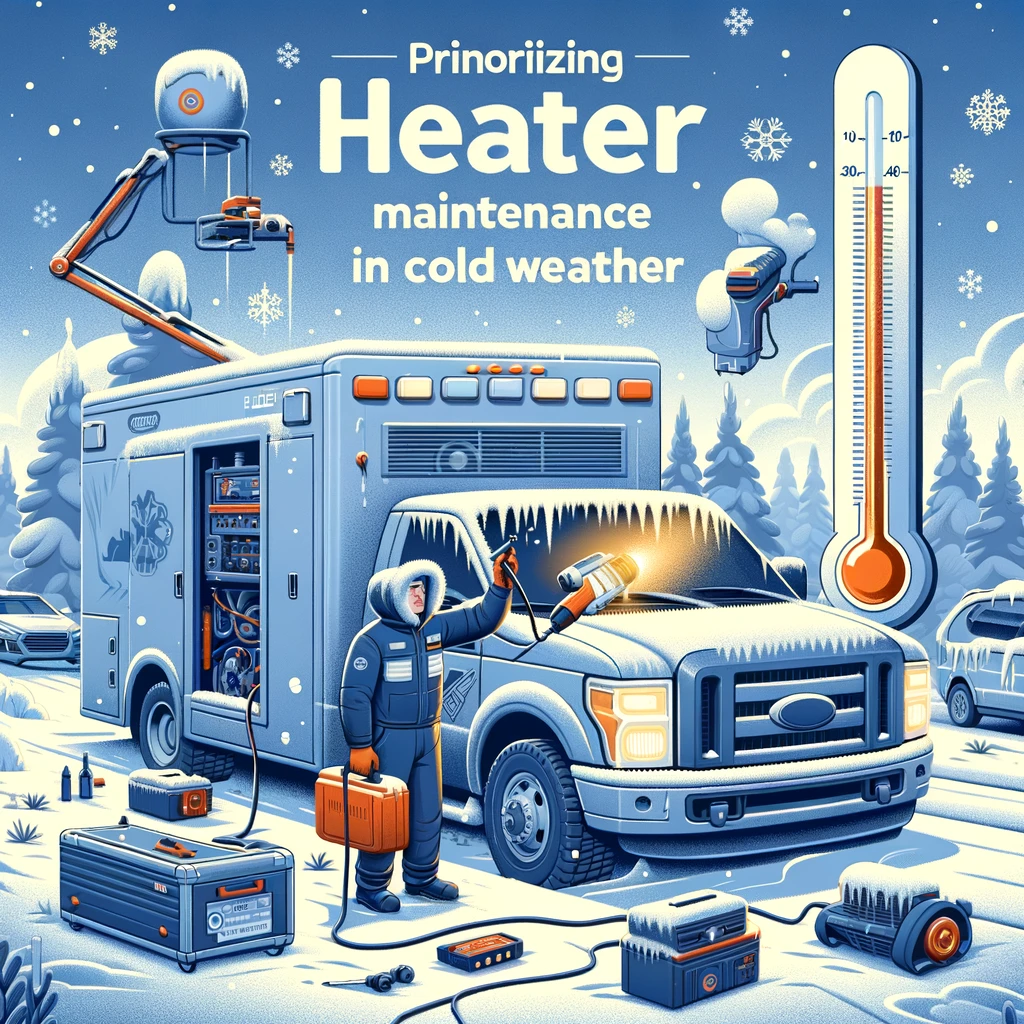
Perform inspections on all squad heaters prior to winter. Repair or replace any components that may fail when put under heavy use.
Adjust service intervals to account for increased operating hours and harsh conditions. Check vehicles more frequently as seasons change.
Educate drivers on proper operation and what to do in case of heat loss. Have emergency plans in place to get drivers safely off the road.
Proactive winter maintenance reduces the risk of breakdowns in sub-zero conditions where safety is a top concern.
Educating Drivers on Proper Heater Operation
For heating systems to deliver their full service life, drivers must use them properly to avoid damage. Therefore, education on proper operation is time well spent.
Instruct drivers to:
- Allow gradual warm-up to operating temperature
- Keep the fan on low until the engine is warm
- Avoid aiming vents at windshields before defrosting
- Report any temperature control or heat loss issues promptly
Ongoing training ensures drivers don’t develop any bad habits that could harm heating components or reduce comfort.
Reducing Costs Through Preventative Maintenance
An effective preventative maintenance program represents one of the best opportunities to control fleet operating costs. Heater upkeep is a prime example.
Well-maintained heaters have minimal unscheduled downtime and road calls. Repairs are made during planned service intervals at lower labor rates.
Proper maintenance extends heater lifespan past vehicle trade cycles in most cases. No premature replacements are needed.
Spending modest amounts on routine care avoids huge bills for emergency repairs down the road. The ROI of preventative maintenance is impressive.
Improving Driver Safety and Comfort
When heaters operate reliably, they keep drivers warm, alert, and focused on the road. Proper maintenance directly contributes to their safety and comfort.
Adequate defrosting prevents dangerous frost and fogging that obscures vision. Stable temperatures reduce driver fatigue on long trips.
Uncomfortably cold or hot conditions wear down drivers and are distracting. Smooth heating improves morale and retention.
Your drivers are your most valuable assets. Investing in their well-being through proper heater care protects that asset.
Complying with Regulations for Heater Emissions
Fleet vehicles are subject to emissions regulations regarding smoke, particulates, and carbon monoxide in exhaust. Heaters play a role in compliance.
Follow OEM procedures for tuning and maintaining heaters to factory specifications. Perform any required emission service actions.
Technicians should be trained to spot and correct exhaust leaks that could allow CO into cabs. Repair any damaged after treatment components.
Document your maintenance diligently to prove compliance if any issues arise during inspections.
Proactive care prevents heater-related emissions failures that could ground vehicles and lead to significant fines.
Troubleshooting Common Diagnostic Codes
OBDII diagnostic trouble codes provide valuable clues during heater troubleshooting. Technicians should be familiar with assessing common heater DTCs:
- P0128 – Coolant Thermostat Below Control Range
- P0126 – Coolant Temperature Sensor Performance
- B1000 – Vehicle Power Relay Short Circuit
- B1001 – Blower Motor Monitor Fault
- B1004 – Blower Speed Circuit Fault
- P0597 – Auxiliary Heater Fuel Metering Fault
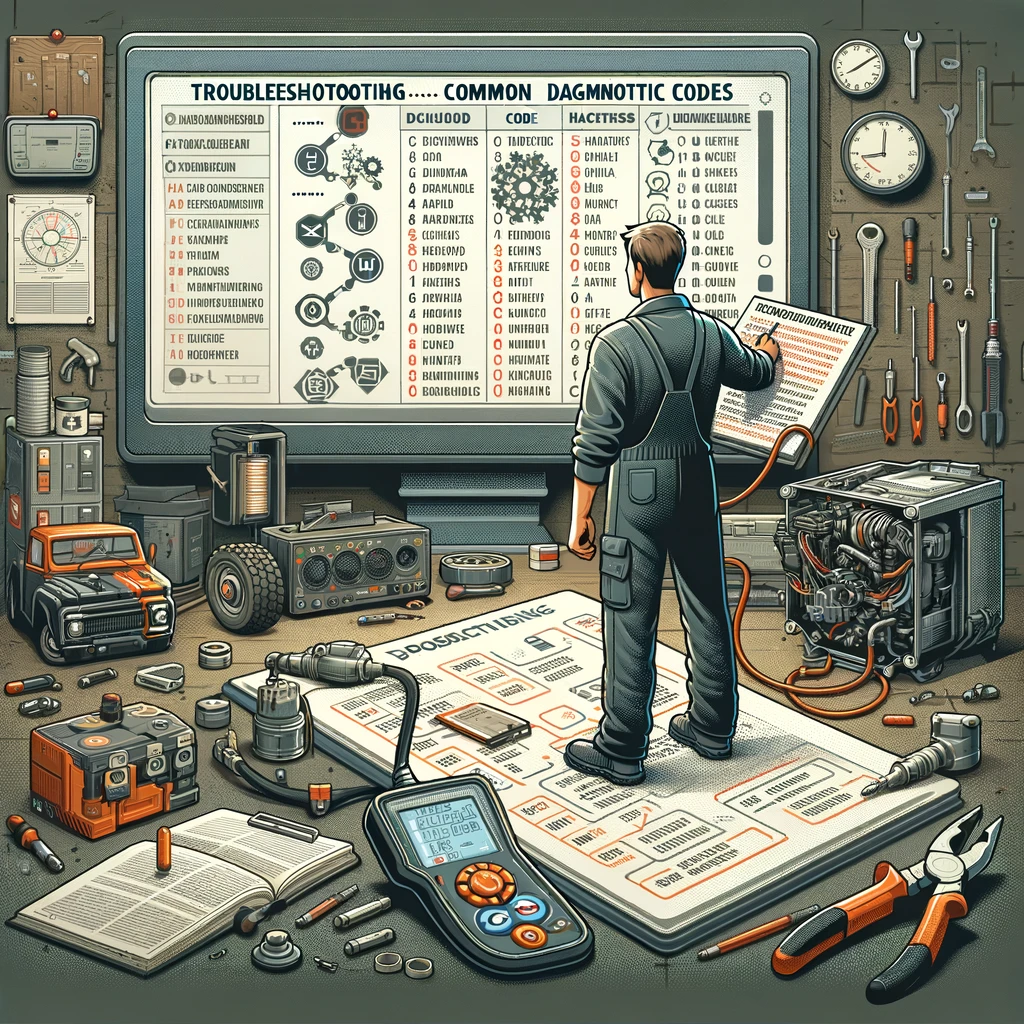
Use DTCs to identify the malfunctioning component. However further testing is needed to confirm the root cause.
Performing Seasonal Heater Inspections
Seasonal temperature fluctuations place extra strain on heating systems. Performing seasonal inspections helps ensure trouble-free operation.
Conduct inspections at the start of winter and summer seasons. Check all components and fluids. Replace filters and hoses showing wear.
Test heaters for proper operation at minimum and maximum settings. Verify defrost capability and temperature regulation.
Seasonal preparation reduces failures when heaters switch from light duty to heavy usage in cold weather or hot climates.
Identifying Time for Heater Core or Burner Replacement
Though designed to last long periods, heater cores and burner assemblies do eventually wear beyond serviceability. Know when they require replacement:
- Heater cores: Leaking, very restricted coolant flow, or severe internal corrosion
- Burner assemblies: Excessive carbon build-up, worn/damaged components, performance decline
Replacement should fix the loss of heat issues not resolved by troubleshooting other components like thermostats or sensors.
Use OEM or OEM-quality parts that match system requirements and tolerances. Proper repair procedures prevent damage.
Sourcing Reliable and Cost-Effective Service Providers
Unless your fleet facility has extensive in-house capabilities, you’ll likely need to utilize outside shops for certain heating repairs. Choose service partners carefully.
Look for commercial repair shops with certified technicians and a solid reputation for heating system work. Check references.
Inspect their tooling and equipment to ensure they can properly diagnose and repair your fleet’s heating technology.
Evaluate parts sourcing, warranties, and invoicing/payment processes. Make sure capabilities and business practices align.
Reliable service partners help control costs while getting vehicles back on the road faster.
Budgeting for Annual Heater Maintenance Costs
Proper fleet budgeting means allocating sufficient funds for annual heater system maintenance based on repair history and trends.
Analyze previous years’ expenditures on heating repairs and parts to estimate averages. Break down by vehicle type/class.
Factor in inflation on parts and labor when projecting future year costs. Account for fleet growth or contraction.
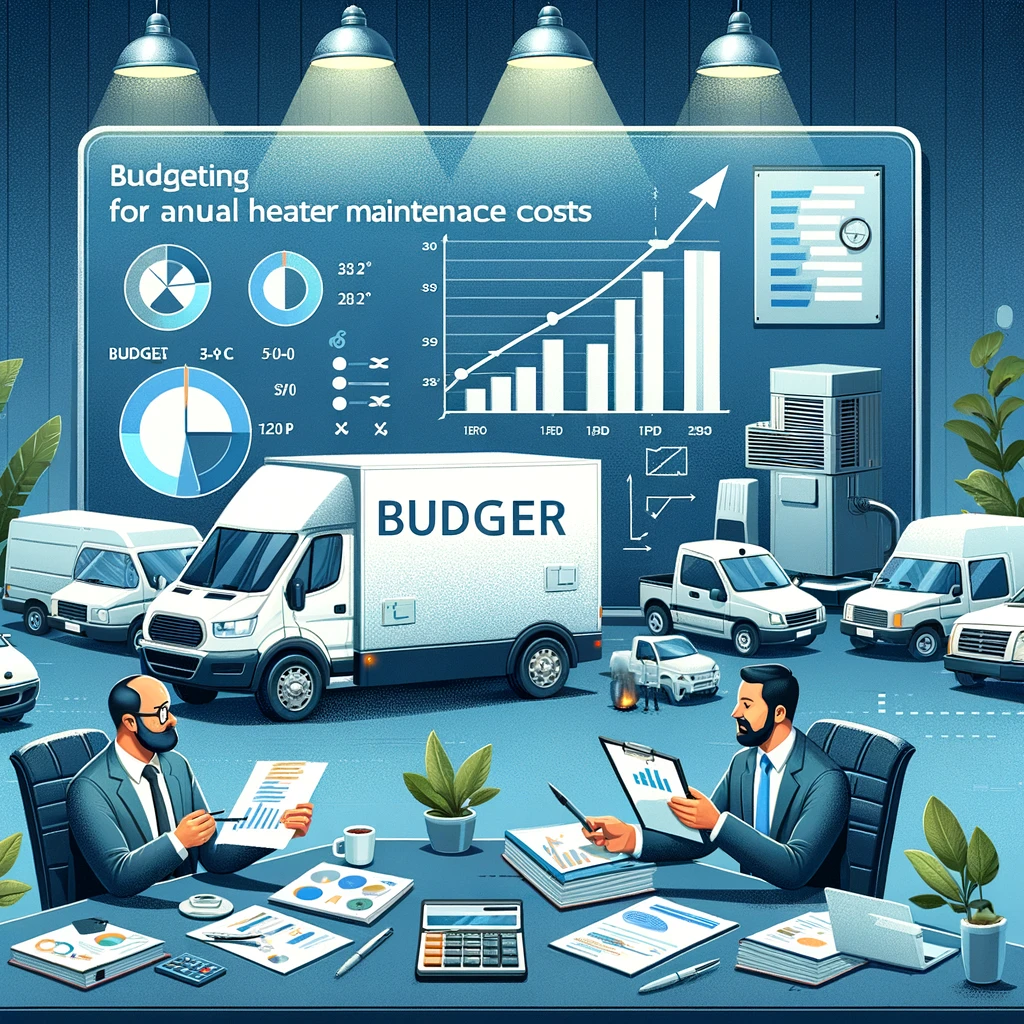
Include projected major repairs or replacements based on mileage-based schedules. Budget 5-10% above projected costs as a contingency.
Accurate budgeting for heating systems helps avoid surprise shortfalls and keeps the fleet running smoothly.
Leveraging Extended Warranties on New Vehicle Purchases
Purchasing extended OEM warranties on new fleet vehicles can effectively control heater repair costs during the coverage period.
Extended warranties allow fleets to fix heaters under warranty rather than paying maintenance budgets. This reduces operating costs.
Review terms to ensure coverage fits your replacement cycles. Negotiate pricing upfront when ordering new units.
Utilize dealership warranties on all eligible repairs. Track expiration dates closely to maximize the value of included maintenance.
Future Heater Technologies and Design Improvements
Heating technology continues advancing with fuel economy, performance and reliability enhancements. Understand these coming improvements:
- Electric heating systems replacing fuel burners
- Increased automation and temperature zone controls
- Active coolant management for faster warm up
- Recirculating/condensing heater cores
- Refractory metal coatings on components
- Remote/predictive diagnostic capabilities
Consider future systems during planning to improve lifecycle costs. Collaborate with suppliers on design changes that benefit your operation.
Conclusion: The Benefits of Proactive Fleet Heater Maintenance
This guide underscores the importance of making heater maintenance a core element of your fleet management strategy. The benefits of proactive care are substantial:
- Increased driver comfort, safety, and productivity
- Maximum uptime with fewer road calls and downtime
- Extended heater lifespan past vehicle replacement cycles
- Lower lifetime repair costs through preventative care
- Reduced liability risks and regulatory issues
- Improved driver recruitment, satisfaction and retention
While requiring diligence and commitment, proper heating system maintenance delivers tangible payoffs for fleets willing to invest in it. Following the best practices outlined here will help optimize your program. Maintain communication and collaborate with drivers, technicians and suppliers to continuously improve. With careful attention over time, your fleet’s heaters will deliver trouble-free operation for many years to come.